Excellence in Cost Management Consulting
At eXworks Consulting, we specialize in transforming operational challenges
into competitive advantages through our focused consulting services.
Dedicated to excellence in cost management, our team empowers organizations to
achieve sustainable financial performance and enhanced product value.
Cost Analysis
Dive deep into the financial aspects of your operations with our Cost Analysis services. We provide thorough evaluations of your spending and resource utilization to identify cost-saving opportunities and areas for efficiency improvement. Our detailed reports and actionable insights enable clients to make informed decisions that bolster their bottom line.
Value Engineering
Maximize your product's market potential with eXworks’ Value Engineering services. By focusing on the function of products and optimizing for cost and performance, our approach not only reduces expenses but also enhances product value. We help you rethink and redesign processes and components, ensuring optimal performance without compromising quality.
Product Cost Down
Achieve significant reductions in your product costs with our targeted Product Cost Down strategies. From initial design to final production, we scrutinize every step of your product development cycle to implement cost-saving measures that do not sacrifice functionality or consumer appeal. Our strategies are designed to ensure that cost efficiency is embedded in your product lifecycle.
Design to Cost
With our Design to Cost services, financial targets are integrated into the design process from the very start. We collaborate closely with your product development teams to align product specifications with predetermined cost objectives. This proactive approach ensures that every design decision supports both cost efficiency and market competitiveness.
Commitment to Client Success
At eXworks Consulting, your success is our success. We are committed to delivering not just solutions but measurable outcomes that drive growth and profitability. Our experts combine industry knowledge with practical experience to offer tailored advice that aligns with your company’s vision and operational goals.
Partner with eXworks Consulting to navigate the complexities of cost management and product optimization. Let us help you turn cost challenges into strategic advantages, ensuring your business thrives in competitive markets. Contact us today to discover how we can assist in achieving your financial and operational goals with precision and innovation.
Method of should-cost calculation

Understanding the Impact of Production Volumes on Cost through Transparent Cost Analysis
In the complex landscape of manufacturing, understanding how production volumes affect costs is crucial for strategic planning and operational efficiency. Transparency in cost analysis plays a pivotal role in this understanding, offering clear insights into the relationship between production scales and their direct impact on unit costs.
The Importance of Transparency in Cost Analysis
Transparent cost analysis provides a detailed breakdown of costs associated with the production process, including materials, labor, overhead, and other indirect expenses. This clarity is essential for identifying how costs behave as production volumes change. It allows companies to see not just the total costs, but how specific cost components vary with changes in production scale.
Volume-Cost Relationship Insights
Economies of Scale
Increased production volumes often lead to economies of scale, where the cost per unit decreases as the quantity produced increases. Transparency in cost analysis helps quantify these savings and identify the volume thresholds necessary to achieve them.
Fixed vs. Variable Costs
Understanding which costs are fixed and which are variable is crucial. Transparent cost analysis reveals how fixed costs, such as equipment and salaries, are amortized over larger production volumes, potentially lowering the per-unit cost. Conversely, it shows how variable costs, like raw materials and energy, fluctuate with production output.
Optimal Production Levels
With transparent cost data, companies can determine the most cost-effective production levels. Analyzing how costs change with volume adjustments can help identify the optimal balance between production capacity and cost efficiency, ensuring that resources are utilized effectively without overproduction or underutilization.
Strategic Decision-Making
Clear, detailed cost insights allow management to make informed decisions about scaling operations. It supports strategic initiatives such as market expansion, product line diversification, and capital investment, aligning them with cost-effective production practices.
Supplier Negotiation and Procurement Strategy
Transparency helps companies understand cost drivers and negotiate better terms with suppliers. Knowing how materials and component costs contribute to overall expenses can leverage bulk purchasing or long-term contracts to reduce costs.
Transparent cost analysis is not just about keeping track of expenses; it's about understanding the dynamics of cost behavior in relation to production volumes. This understanding is critical for making informed decisions that enhance operational efficiency and profitability. By embracing transparency, companies can strategically manage production levels, optimize costs, and improve their competitive edge in the marketplace.
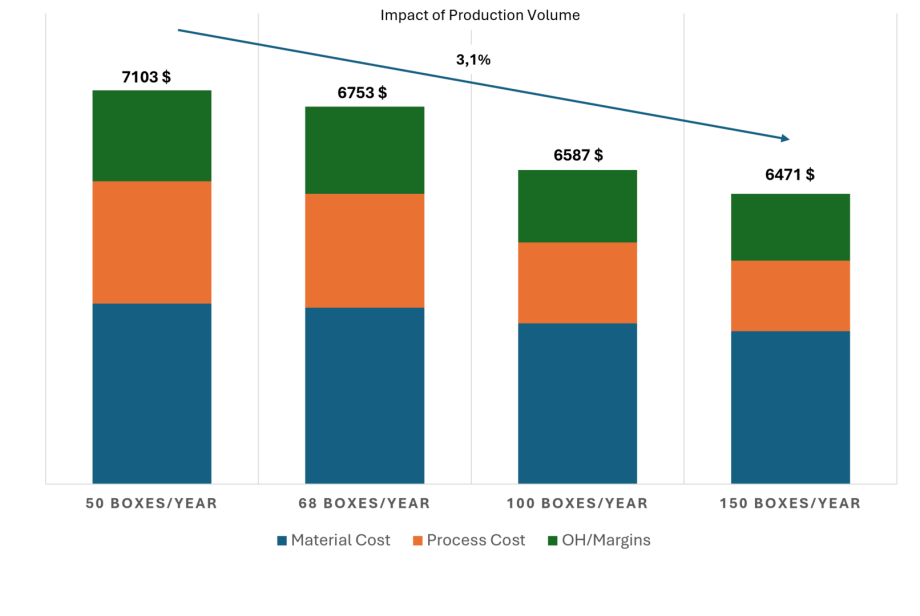